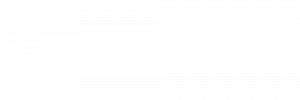
Cell rubber sealing gaskets
Special seals, sealing cushions, flat gaskets & sealing tape
Cellular rubber is the perfect material for gaskets and sealing cushions of all kinds. Most cell rubbers are closed-cell, soft and elastic. Seals made of cell rubber are impermeable to water and adapt seamlessly and flexibly to their respective operating environment. An outer skin like e.g. with foam rubber is not necessary. Cellular rubber seals reliably even without an outer skin.
All cell rubber qualities can be split, cut, punched, glued, milled and water jet cut. In addition, the material can be coated, perforated and laminated, for example with a self-adhesive film for aiding assembly. Contact us! We deliver your seal or sealing cushion made of cellular rubber!
Cell rubber gasket types at a glance
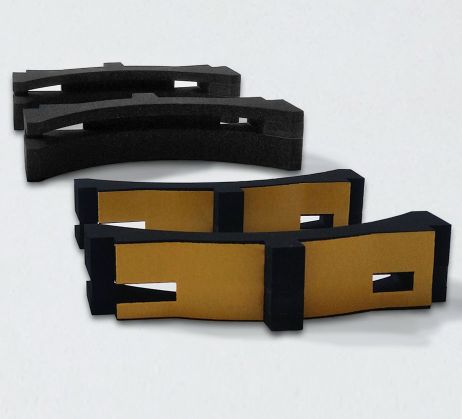
3D special sealing gaskets
Cell rubber sealing gaskets with 3D geometry are a windowSafe® core competence.
Manufacturing is often complex and technically demanding. Some special seals made of cellular rubber can be produced using a 3D water jet cutter. In other cases a blank undergoes several operations or separate individual parts are glued together. In particularly complicated cases all three manufacturing processes will be combined.
Examples of cell rubber sealing gaskets that require 3D manufacturing:
- Seals need to have self-adhesive coating on partial surfaces.
- Sealing gaskets need undercuts or recesses.
- Seals need to be equipped with holes to make later assembly easier.
Send us your request for a 3D sealing gaskets with a drawing: info@windowsafe.de.
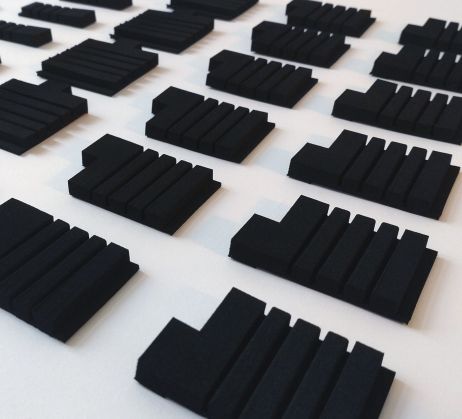
Cell rubber sealing cushions
3D sealing gaskets in all their complexity are not always required. 2D gaskets made of cell rubber also seal reliably.
Especially in window and facade construction the classic sealing cushion is ever popular: two-dimensional and without self-adhesive coating. Instead with grooves and rills so that it can be inserted precisely into the corresponding aluminium, wood or plastic profiles.
The soft cellular rubber material seamlessly closes gaps and voids and permanently ensures that neither air nor water can penetrate. Cellular rubber sealing cushions can be attached quickly and safely.
Time-consuming manual sealing work and rework can be avoided. Assembly times and therefore costs are reduced.
Send us your request for a cell rubber sealing cushion: info@windowsafe.de.
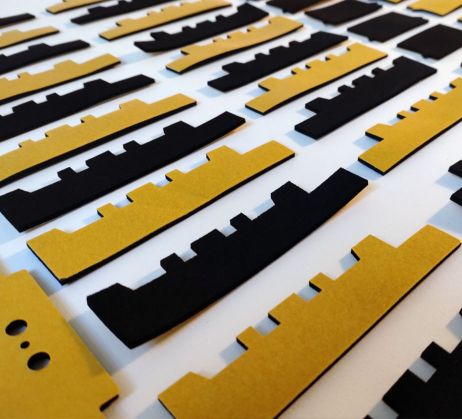
Cell rubber flat gaskets
The general rule is: the more complex the geometry of a seal the more demanding the manufacturing.
However, many seals are not that complicated and can therefore be produced in large quantities with very low costs using standard processes. The best example of this: flat gaskets.
Flat gaskets made of cell rubber can either be cut by water jet or punched. In both cases, production is very quick and therefore particularly economical.
In addition there is the kiss-cut option for both processes when it comes to self-adhesive flat gaskets. Here the parts remain on the uncut adhesive cover film and can later be easily removed from the backing sheet quickly and without leaving any residue. [ More info on Kiss-Cut]
You need flat gaskets made of cellular rubber or another material?
Send us your request: info@windowsafe.de.
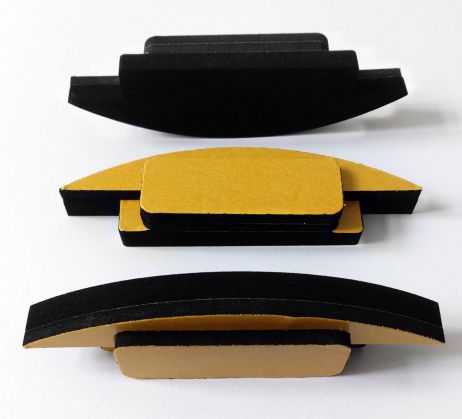
Self-adhesive sealing gaskets
Many sealing gaskets made of cellular rubber are equipped with self-adhesives to make installation easier. The adhesive side prevents slipping while assembling other elements or falling off sloping or vertical surfaces. The seal can be positioned precisely and thanks to its self-adhesive layer stays in place permanently.
Various adhesive films are available. The windowSafe® standard self-adhesive lamination is a solvent-free, environmentally friendly double-sided adhesive tape on a special paper backing. The product is physiologically harmless and has good aging as well as weather resistance.
- Adhesive: acrylate
- Cover: silicone paper, yellow
- Use: as assembly aid ( )
Send us you request concerning self-adhesive sealing gaskets: info@windowsafe.de.
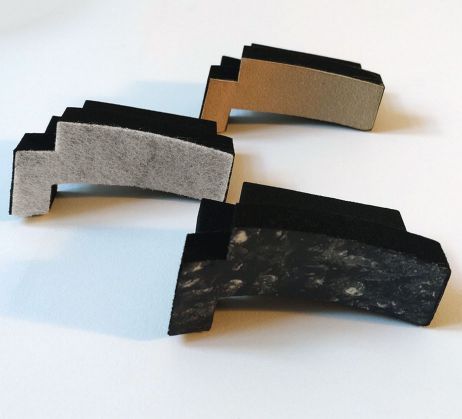
Coated sealing gaskets
The natural properties of a material can be supported and expanded through coating. With cellular rubber that usually means either an improvement in temperature resistance or in lubricity.
Temperature resistance: a coating with PTFE is recommended to optimize temperature resistance. The material is applied in a liquid state and forms a thin, flexible outer skin that can withstand very high temperatures without affecting the tightness of the cellular rubber.
Lubricity: the coating with liquid PTFE can also be used for improved sliding properties. In addition partial coating with solid materials is possible (e.g. solid PTFE, rubber, plastic, felt, etc.). Placed strategically they prevent excessive friction between the sealing gasket and its operating environment.
For more coating options please contact us: info@windowsafe.de.
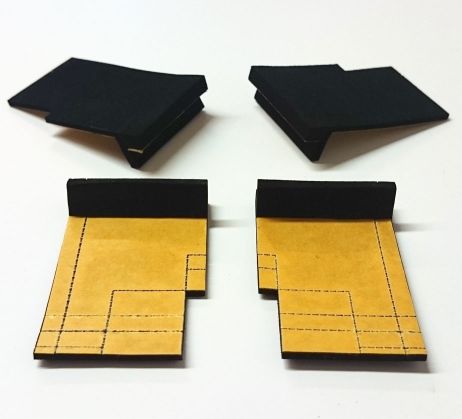
Perforated sealing gaskets
Perforated sealing gaskets are the all-purpose tool among sealing products.
Instead of two, three or more different seal geometries only one geometry is manufactured and fitted with perforations. During assembly the seal that is needed is "made" by detaching parts that are not required.
However bevor fitting cellular rubber gaskets with perforations the following points should be taken into account:
- The gasket should not be so thick that the functionality of the perforation lines suffers.
- The thinner the cellular rubber the finer the perforations can be.
- Please check whether thick perforation cuts may affect the tightness of the sealing gasket.
Any questions? Please feel free to contact us: info@windowsafe.de.
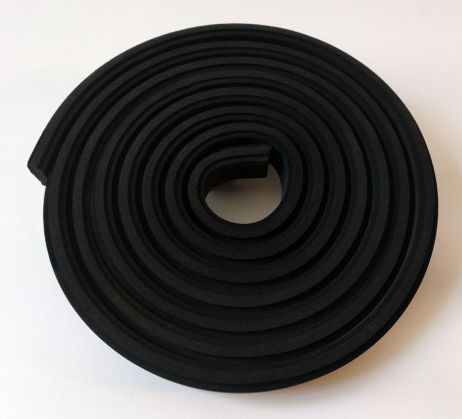
Cell rubber sealing tape
Sealing tape made of cellular rubber is not extruded but cut by the meter.
For this reason tape lengths are either limited to the dimensions of the raw material block or require bonding. Also complex geometries that go beyond simple rectangular shapes are difficult or even impossible to manufacture.
Nevertheless cell rubber sealing tape has advantages over extrusion profiles:
- No tools are required.
- There are no minimum quantities to consider.
- Cellular rubber tapes are tight and - unlike sponge rubber profiles - do not require an extra outer skin.
You need a closed-cell profile with complex geometry and no adhesive joints?
Than an extruded PE foam profile might be your solution.
About cellular rubber
Cellular rubber is a foam-shaped elastomer that is primarily used for sealing, insulating and providing buffering. Since the material has cells that are closed on all sides water and air impermeability of up to 99.9% can be achieved.
The technical properties of cellular rubber at a glance
- excellent sealing properties
- low thermal conductibility (ca. 0,04 W/mK)
- excellent compressibility
- excellent insulation properties
- very low water absorption
- flexible processing options
- high ageing and temperature resistance (EPDM)
- high flame retardancy and oil resistance (CR/NBR)
What makes cellular rubber so special as a material is its closed cells. It is therefore preferably used where something needs to be permanently sealed, for example in windows and facades or in mechanical engineering. Its popularity as a material for sealing gaskets and cushions has led to a variety of cellular rubber qualities that can do much more than just seal. There is:
- a wide range of material hardness: from super soft (10° Shore 00) to hard (80° Shore 00)
- food-grade cell rubber qualities
- self-extinguishing cell rubber qualities
- temperature resistant cell rubbers
- qualities with a variety of certifications & approvals (UL94, FMVSS, ISO, REACH, etc.)
Even sustainable cellular rubbers are slowly coming onto the market - i.e. qualities that are made from renewable raw materials, contain recycled content or are easily recyclable themselves.
Cellular rubber is produced via expansion process based on natural and/or synthetic rubbers. The most common are EPDM, CR, NBR and NR/SBR. The respective blend determines the material properties of the end product.
Natural rubber (NR) has high tensile and compressive strength. EPDM (also known as APTK) is very resistant to aging, ozone, light & weathering and is therefore particularly suitable for outdoor use. Chloroprene rubber (CR) meets high requirements in terms of temperature, flammability, oil, acid, alkali and grease resistance. Nitrile rubber (abbreviation NBR) is an oil-resistant and partially gasoline-resistant quality that is also very good in terms of weather and ozone resistance but flammable.
windowSafe® cell rubber standard qualities (selection)
Cellular rubber EPDM
> color: black
> hardness: 40° Shore 00 (± 10)
> density: 175 kg/m³
> vacuum water absorption: < 5%
> excellent weather & ageing resistance
Cellular rubber EPDM (very soft)
> color: black
> hardness: 20° Shore 00 (± 5)
> density: 75 kg/m³
> vacuum water absorption: 11%
Cellular rubber CR
> color: black
> density: 150 - 200 kg/m³
> vacuum water absorption: 3,5%
> good temperature resistance (up to + 145°C short-term)
We can offer many more cell rubber qualities with differing properties:
- colors: black, grey, light beige
- shore hardness from ca. 20° up to 80° Shore 00
- density from ca. 75 kg/m³ up to ca. 500 kg/m³
- closed-celled & half closed-celled types
- various qualities e.g. EPDM, CR, NBR and blends
Send us your request: info@windowsafe.de.
Both cellular rubber and sponge rubber are processed forms of celled rubber. Both are made from the same raw materials (e.g. EPDM) via expansion. The main differences lie in the cell structure as well as in the processing options.
Cell structure
Either material is expanded using blowing agents. They are therefore often referred to as foam rubber. While cellular rubber usually has closed cells sponge rubber is a mixed-cell material.
In order to seal optimally sponge rubber needs a closed outer skin. If this is damaged it will affect the sealing function. Cellular rubber on the other hand is tight even without an outer skin. During processing the external cells are cut but water cannot penetrate further into the material. The surface made of cut cells also has advantages: it is non-slip and well suited for bonding with adhesives. For this reason cellular rubber is often preferred to sponge rubber in the sealing sector.
Processing
Both cellular rubber and sponge rubber can be split, cut and punched. Seals and sealing cushions are cut or punched out of raw material in block or plate form.
Unlike cellular rubber sponge rubber can also be shaped directly: for example by extrusion. Here the raw material is pressed (extruded) through a shaping opening and a profile with the corresponding cross-section is created. Since cellular rubber is not extruded, foam rubber profiles are usually made of sponge rubber.
Cell rubber & sponge rubber at a glance
Cell rubber
- excellent sealing properties
- low thermal conductivity
- excellent compressibility
- good insulation properties
- vacuum water absorption <5% (without outer skin)
Sponge rubber
- high compressive elasticity
- high compressibility
- good insulation properties
- flexible processing options (i.e. extrusion)
It should be noted that "foam rubber", "sponge rubber" and "cell rubber" are often used synonymously which can lead to confusion. (See also “What is the difference between cellular rubber and sponge rubber?”)
Furthermore the term “foam rubber” is close to “foam”. There is another risk of confusion here. Because “foam materials” such as PE foam are a completely different group of materials with correspondingly different properties.
The use of different terms has grown historically. The first industrially foamed rubber material came onto the market in Europe at the end of the 19th century. It was open-celled and called "sponge rubber". This sponge rubber version - the open-cell, mostly orange material based on natural rubber (NR) - is still produced and used today in an optimized form.
While a further developed mixed-cell quality with an outer skin was later called "Moosgummi" in Germany, in English usage however the term “sponge rubber” remained. Closed-cell cellular rubber became ready for the market even later and was listed separately in both languages as "cell(ular) rubber" or "Zellkautschuk" respectively.
On this website the different terms are used as following:
Cellular / cell rubber = closed-cell foam rubber quality (in German: "Zellkautschuk")
Sponge rubber = mixed-cell foam rubber quality (in German: "Moosgummi")
Foam rubber = all rubber qualities with celled structur (open, closed, mixed)
Since one of the special properties of cellular rubber is to achieve water- and air tightness of up to 99.9% most cellular rubber qualities are closed-cell.
Though there are cell rubbers whose cells are not completely closed. This is usually due to their softness. The softer a cellular material is the larger its pores usually are. And the larger the cells in the material become the more difficult it is to keep them closed.
Many cellular rubbers below a Shore hardness (00) of 25 are no longer completely closed-cell. The water absorption in a vacuum is over 5% for these qualities.
However this does not mean that these materials are not suitable for sealing gaskets and cushions. Super-soft cellular rubber can be compressed very tightly and is thus able - with its cells are solidly pressed - to seal very well.
So if a sealing gasket is used on a very irregular surface or very strongly compressed it is safe to use a super-soft cellular rubber quality with cells that are not 100% closed.
windowSafe® cell rubber EPDM (super soft)
- color: black
- density: 95 kg/m³
- vacuum water absorption: ca. 10%
- coarse-pored, super soft and compressible
- excellent adaptability to irregular surfaces
- even with low compression (≤ 10%) waterproof and airtight
All cellular rubber qualities can be split, cut, punched, glued and cut by water jet.
It should always be borne in mind that the material is a cellular and comparatively soft. The processing tolerances are accordingly different in comparison to e.g. soft rubber. However the larger dimensional tolerances are usually compensated for by the softness and flexibility of the material.
The most important manufacturing processes briefly explained:
Splitting
By splitting the cellular rubber - usually in form of sheets or plates - is cut to the processing thickness. For example a cellular rubber sheet with dimensions of 1,000 x 1,000 mm and a thickness of 40 mm can be split into 4 sheets with dimensions of 1,000 x 1,000 x 10 mm. Since product thickness varies greatly splitting is often the first step in the manufacturing process.
Punching
Punching (also called die cutting) is a manufacturing method that is often used with cellular rubber. Here a metal cutting die is made first. The die is pressed through the material. This creates parts in the desired shape. The resulting cutting edges are – unlike with water jet cutting – free of grooves. However slight concavity may occur with larger material thicknesses.
Water jet cutting
During water jet cutting the cellular rubber is separated using a high-pressure water jet. Since the contours can be programmed directly into the machine there are no costs for tools or molds. Even complex contours are no problem. In contrast to punching concave cutting edges are not a problem even with larger material thicknesses. However grooves can form at the cutting edges due to the water jet breaking out.
The so-called “kiss cutting” is a special punching process that can be used to manufacture cellular rubber gaskets.
Here two or more layers of material lying on top of each other are processed but not all layers are affected by the punching process. Usually the bottom layer is only touched gently: "kissed" instead of "cut".
This is used in particular for the production of self-adhesive seals. The material is first covered on one side with self-adhesive film. During the subsequent punching process the cellular rubber and adhesive are cut through but not the adhesive's backing paper.
The result is a sheet with stamped parts that can later be easily removed and applied.
The alternative for initial & small batches: Waterjet Kiss-Cut!
The process is different - but the result is the same. In addition Waterjet Kiss-Cut has decisive advantages:
+ There are no tool costs.
+ Both large and small quantities can be manufactured economically.
+ Waterjet Kiss-Cut is very suitable for complex parts as well as for very soft and open-celled materials.
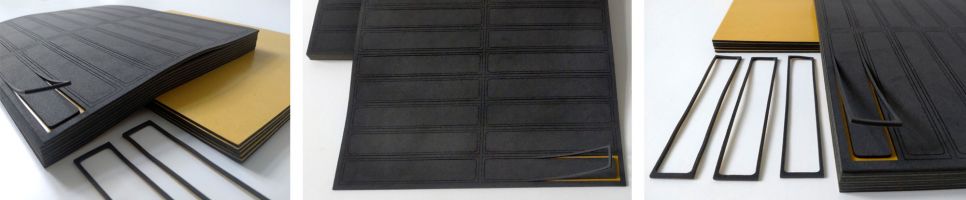
Sustainability is an important issue in most industries increasingly and rightly so. Unlike many other products the focus of sealing gaskets and cushions lies primarily on functionality though. Since this almost always includes longevity, questions about e.g. recyclability are still of secondary importance.
Nevertheless the construction industry and other sectors in which seals are used are thinking more and more about renewable materials, CO2 reduction and circular economy.
When it comes to cell rubber there are now qualities available that are partially made of renewable or recycled raw materials. However there is currently no 100% sustainable cellular rubber. This is primarily due to the specific technical requirements that e.g. seals made of cellular rubber must meet and which cannot (yet) be reproduced using sustainable raw material components.
You have questions or are you interested in seals and sealing cushions made from sustainable cellular rubber? Contact us. We would be happy to advise you.